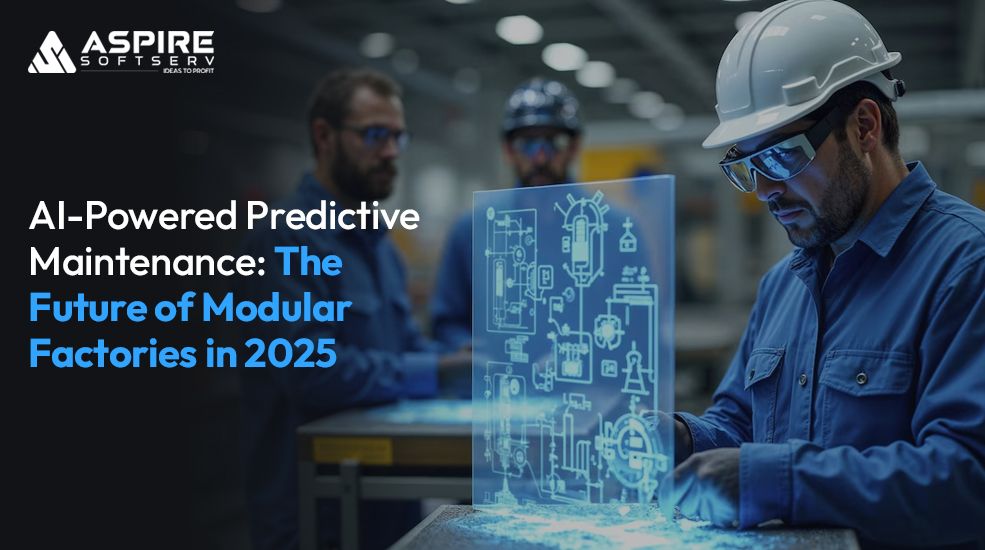
Modular factories, built for flexibility and rapid reconfiguration, are at the heart of modern manufacturing. These facilities switch between producing car parts one week and medical devices the next, adapting to market demands. Yet, their complex equipment poses a challenge: how do you keep everything running smoothly without costly delays? Predictive maintenance, driven by artificial intelligence, offers a solution. By analysing machine data in real time, AI predicts when equipment might fail, allowing workers to act before issues disrupt production. In 2025, this technology is evolving with trends like Industry 5.0, sustainability, and digital twins, reshaping how factories operate. This article explores where predictive maintenance is headed and what it means for modular manufacturing.
What Is AI-Powered Predictive Maintenance?
Picture a factory where every machine—robotic arms, conveyors, cooling systems—sends data to a central system. Sensors track details like temperature, vibration, or power usage. AI Development Services analyse this information, spotting patterns that signal potential problems. For example, a slight increase in motor vibration might seem minor, but when paired with a drop in efficiency, it could point to wear. The system flags this, and technicians fix it during a planned break, avoiding a shutdown.
Unlike traditional maintenance, which follows fixed schedules or reacts to breakdowns, predictive maintenance works in real time. It’s especially valuable in modular factories, where equipment changes often. By catching issues early, AI reduces downtime and keeps production on track. Data Engineering plays a key role here, organising vast amounts of sensor data into usable insights. Without clear data pipelines, AI couldn’t make accurate predictions. This combination of AI and data management is setting the stage for smarter factories.
Why Predictive Maintenance Matters in 2025
Modular factories thrive on adaptability, but unexpected equipment failures can halt production and raise costs. Predictive maintenance addresses this by monitoring machines continuously. Consider a factory making electric vehicle batteries. If a robotic welder starts producing inconsistent joints, it could lead to faulty batteries and expensive recalls. AI spots early signs—like irregular weld patterns—and alerts technicians to recalibrate the machine, saving time and resources.
In 2025, predictive maintenance ties into broader trends. Industry 5.0 emphasizes human-machine collaboration, where AI supports workers rather than replacing them. Technicians use AI predictions to focus on high-value tasks, like optimizing production, instead of rushing to fix breakdowns. Sustainability is another driver. By fixing equipment before it fails, factories use less energy and produce less waste, aligning with global eco-friendly goals. Digital twins—virtual models of physical machines—also play a role. AI analyzes digital twin data to simulate maintenance scenarios, making predictions even sharper. These trends make predictive maintenance a cornerstone of modern manufacturing.
Real-World Impact
Predictive maintenance is already proving its worth. In a European factory producing wind turbine blades, AI monitored molding machines for pressure and material flow. When one machine showed irregular patterns, the system predicted a valve issue days in advance. Technicians replaced it during a scheduled pause, avoiding a costly halt. This cut maintenance costs by 18%. In a North American electronics plant, AI tracked 3D printers for overheating risks. By adjusting print schedules, the factory reduced defects by 12% and extended equipment life.
These examples show how AI adapts to different setups. Whether it’s heavy machinery or precision tools, AI Development Services learn from each factory’s unique data, improving predictions over time. Data Engineering ensures sensor data is clean and accessible, enabling AI to focus on what matters. As factories adopt these systems, they see fewer disruptions and better efficiency.
Challenges to Overcome
Predictive maintenance isn’t flawless. One hurdle is data overload. A typical factory has thousands of sensors, generating massive information. Sorting through it to find relevant signals—like vibration spikes—takes effort. Data Engineering helps by prioritizing key metrics and streamlining analysis. Over time, AI learns which data points matter most, refining its focus.
Another challenge is integration. Modular factories often use equipment from different manufacturers, each with its own software. Getting these systems to share data can be tough. Universal protocols, like MQTT or OPC UA, help machines communicate, but setting them up requires planning. Companies are solving this by standardizing data formats across their facilities.
Workers also need convincing. Some hesitate to trust AI over manual inspections, especially if they’ve relied on experience for years. Training programs that show real examples—like how AI caught a failure—build confidence. Involving technicians in the process, such as reviewing AI alerts before acting, eases the transition. These steps ensure predictive maintenance works for both machines and people.
The Road Ahead
By 2025, predictive maintenance is moving beyond fixing machines to transforming factories. Digital twins are a game-changer. These virtual replicas let AI test maintenance strategies without touching real equipment. For example, a digital twin of a conveyor could simulate how adjusting its speed affects wear, helping AI predict failures more accurately. As sensors get cheaper, factories can collect finer data, sharpening these models.
Industry 5.0 pushes this further, blending AI with human expertise. Workers use AI insights to make strategic decisions, like redesigning production layouts for efficiency. Sustainability remains a focus. Predictive maintenance cuts energy use by keeping machines in top shape, supporting net-zero goals. Smaller factories are also joining in, thanks to affordable AI systems that don’t require massive budgets. Aspire SoftServ, for instance, is exploring how these trends can streamline operations without heavy costs.
Wireless tech, like 5G, is speeding things up. It lets AI process data faster, even in large factories. Some researchers are even testing self-adjusting machines that use AI to tweak settings—like slowing a motor to reduce strain. While early, this could make factories more resilient. For now, the biggest win is scalability. From small workshops to global plants, predictive maintenance is becoming accessible, helping manufacturers stay competitive.
Why This Matters to Manufacturers
Predictive maintenance isn’t about replacing workers—it’s about giving them better tools. Technicians can focus on improving processes rather than fighting fires. Managers gain confidence knowing their equipment is monitored 24/7. For modular factories, this means staying agile in a fast-changing market.
If you’re new to this, start small. Test AI on one production line and track the results. You’ll likely see fewer delays and lower costs within months. Then, expand to other areas, using AI insights to fine-tune your operations. Aspire SoftServ has seen how these systems help manufacturers adapt, and the potential is clear: smarter factories that run smoothly and sustainably.
Conclusion
Want to dive deeper into predictive maintenance or Industry 5.0? Share your thoughts or experiences in the comments—we’d love to hear how you’re navigating modular manufacturing. For more insights, connect with our team at [email protected] . Let’s discuss the future of smart factories together!